Laser Illumination
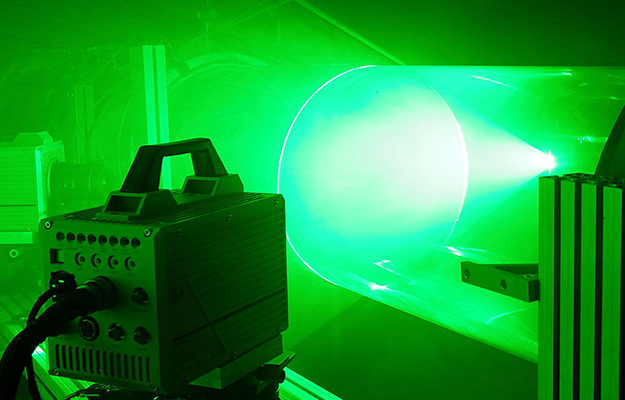
Laser Illumination
The short pulse widths, narrow spectral range and high light intensity offered by laser light sources provides the opportunity for unique imaging techniques when combined with high-speed cameras. To achieve good quality images equal consideration should be given to the illumination source as to the camera resolution and sensitivity. If you have an incorrectly lit subject the resulting image will always be poor. There are a wide range of light sources suitable for most high-speed imaging applications; however, some applications may require something utilizing a laser. For example, laser illumination would help eliminate excessive motion blur.
Most high-speed cameras have an electronic global shutter offering exposure durations down to a few microseconds; however, where a given subject is moving at extreme velocities relative to the field of view, motion blur becomes more of an issue. A high-repetition rate pulsed laser can provide effective shutter durations typically in the range of 30ns – 250ns at frequencies up to around 50kHz without the need for an image intensifier (you will need to match the laser frequency to that of your camera frame rate). Typical applications requiring this level of shuttering could be ballistics, where velocities in excess of 700m/s are common or working at high magnification where the effect of any movement is amplified.
Additional Considerations
Subjects imaged using high-speed cameras require large amounts of light to illuminate them, and with light comes heat. It is important to consider if your test subject should be exposed to these high light levels for extended periods of time as the subject will get hot causing its properties to change. For example, if imaging the production of fiber, it is likely that the heat from the lights will melt the fibers as they are being produced. If impact testing a plastic part, the light will warm this part and make it more elastic thus putting the validity of the test in question. To avoid this a pulsed laser could be used as a light source so an equivalent amount of light can be condensed into a very short period reducing the amount of heat. It is important to note that small areas of interest there are now commercially available pulsed LED light sources that may also be suitable. These will be less expensive than a laser and safe to use in any environment.
Events such as welding, combustion or explosions will naturally saturate or “white-out” a camera image. In order to properly capture these subjects, you need to remove all or most of this unwanted light. There are two different ways to accomplish this, and dependent upon the brightness of the subject you may need to use a combination of both. The easiest way to understand the principals involved is to consider this scenario – you are studying a rapid burning process such as a domestic firework. If there were not an issue with the bright light you could use conventional illumination. However, as the subject does emit this bright light additional components are required.
Spectral filtering– The light emitted from a combustion process will cover a broad spectrum of light. By placing filters on the camera to block most of the light at particular wavelengths such as toward UV and IR this intensity will be reduced. However, it may also reduce the intensity of the light source you are using for illumination so a more powerful source will be required. The solution to this problem is to use a laser to illuminate the subject and place a filter on your camera that will only pass a very narrow band of wavelengths (typically +/-5nm) about the single wavelength of the laser. Of course, there may be a small amount of light emitted by the subject that falls within the band pass of the filter, but the laser should dominate this.
Temporal filtering– Each image taken by a camera has a given exposure length. A long exposure will result in a brighter image. By reducing the length of the exposure, you can reduce the brightness of the image. It may be that even with spectral filtering a long exposure allows sufficient light through the filter to still saturate the image. If this is the case, reducing the exposure by using the electronic global shutter will reduce the light level. If the pulse width of the illumination laser is only 1µs, reducing the exposure time to 2µs will significantly reduce the intensity of the light but will have zero effect on the brightness of the laser. In extreme cases where the shutter time of the camera is still too long, an image intensifier may be fitted to the camera to permit the exposure to be reduced to a length only a fraction longer than that of the laser pulse. Image intensifiers are high cost items and require very careful operation so are used in only a few cases.
Only lasers have the ability to be focused to a thin ‘sheet’ of light that can be projected over a useful distance. Why use a light sheet? Light sheets permit you to visualize a cross section of a flow or spray. Particles entrained in the flow, scatter light from the laser, which permits them to be imaged by the camera. If the particles only move a short distance before the next image is taken you can visualize the movement of this flow. Higher flow velocities will require higher frame rates to maintain a small particle displacement – typically no more than 50 pixels – larger than this will result in a less fluid view of the motion. By having a thin ‘sheet’ of laser light you can define precisely the plane within your flow you are imaging.
You can build on this technique to map the instantaneous velocity of the entire flow field being imaged by using a technique known as PIV or Particle Image Velocimetry. Software is used to calculate the distance the particles travel and by including a linear calibration such as mm/pixel and the time interval between images you can obtain the velocity in m/s. Some flows such as sprays are ‘self-seeded’ i.e. they already have particles present that can be imaged, other flows such as air or water flows may require ‘seeding’ or ‘tracer’ particles to be introduced. These particles are carefully selected based on their physical size, mass and light scattering properties so that they have no negative influence on the flow they are tracing whilst providing a bright reflection that the camera can image.
Droplet by Droplet - Scientists test the protective effect of different materials for face masks against the virus
In Southeast Asia they have become the norm. In Europe, the wearing of simple face masks, whether surgical masks or self-stitched, is under discussion. Opinions on what protection these masks actually offer still differ widely, even within the scientific community. It will be some time before there are really comprehensive and internationally confirmed scientific studies on this subject. “But in my opinion, we as a society cannot afford to wait until this data is available before making a decision,” says Prof. Dr. Oliver Paschereit, head of the Department of Fluid Mechanics at the TU Berlin, who is now conducting scientific tests on the protective effect of face masks as part of a newly applied for project. The idea for the project was born during a telephone conversation with his group leader, Dr. Sebastian Schimek: “Couldn’t our scientific expertise in the field of fluid mechanics contribute to enriching the discussion about the wearing of masks with scientific facts? It was during this telephone call that we developed the basic outlines of the project.”
Observation of laser-induced elastic waves in agar skin phantoms using a high-speed camera and a laser-beam-deflection probe
We present an optical study of elastic wave propagation inside skin phantoms consisting of agar gel as induced by an Er:YAG (wavelength of 2.94 μm) laser pulse. A laser-beam-deflection probe is used to measure ultrasonic propagation and a high-speed camera is used to record displacements in ablation-induced elastic transients. These measurements are further analyzed with a custom developed image recognition algorithm utilizing the methods of particle image velocimetry and spline interpolation to determine point trajectories, material displacement and strain during the passing of the transients.
Optical-flow-based background-oriented schlieren technique for measuring a laser-induced underwater shock wave
The background-oriented schlieren (BOS) technique with the physics-based optical flow method (OF-BOS) is developed for measuring the pressure field of a laser-induced underwater shock wave. Compared to BOS with the conventional cross-correlation method that is also applied for particle image velocimetry (here called PIV-BOS), by using the OF-BOS, the displacement field generated by a small density gradient in water can be obtained at the spatial resolution of one vector per pixel. The corresponding density and pressure fields can be further extracted. It is demonstrated in particular that the sufficiently high spatial resolution of the extracted displacement vector field is required in the tomographic reconstruction to correctly infer the pressure field of the spherical underwater shock wave. The capability of the OF-BOS method is critically evaluated based on synchronized hydrophone measurements. Special emphasis is placed on direct comparison between the OF-BOS and PIV-BOS methods.